Xinfa-hitsauslaitteilla on korkea laatu ja alhainen hinta. Lisätietoja on osoitteessa:Hitsaus- ja leikkausvalmistajat – Kiinan hitsaus- ja leikkaustehdas ja toimittajat (xinfatools.com)
4. Kaarevat kuopat
Se on alaspäin liukuva ilmiö hitsin lopussa, joka paitsi heikentää hitsin lujuutta, myös aiheuttaa halkeamia jäähtymisen aikana.
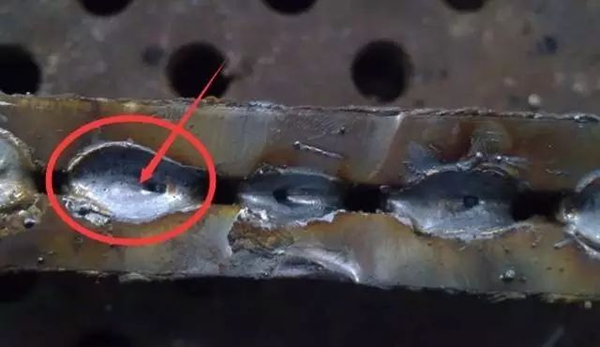
4.1 Syyt:
Pääasiassa valokaaren sammutusaika on hitsauksen lopussa liian lyhyt tai ohuiden levyjen hitsauksessa käytetty virta on liian suuri.
4.2 Ennaltaehkäisevät toimenpiteet:
Kun hitsaus on valmis, anna elektrodin olla hetken aikaa tai tee useita ympyräliikkeitä. Älä pysäytä kaarta äkillisesti, jotta metallia on riittävästi täyttämään sula altaan. Varmista sopiva virta hitsauksen aikana. Pääkomponentit voidaan varustaa kaarenkäynnistyslevyillä, jotka johtavat valokaarikuopan pois hitsauksesta.
5. Kuonan sisällyttäminen
5.1 Ilmiö: Ei-metallisia sulkeumia, kuten oksideja, nitridejä, sulfideja, fosfideja jne., löydetään hitsistä ainetta rikkomattomien kokeiden avulla, jolloin ne muodostavat erilaisia epäsäännöllisiä muotoja, ja yleiset ovat kartiomaisia, neulan muotoisia ja muita kuonasulkeumat. Metallihitsauksissa olevat kuonasulkeumat vähentävät metallirakenteiden plastisuutta ja sitkeyttä sekä lisäävät jännitystä, mikä johtaa kylmän ja kuuman haurauttamiseen, joka on helppo murtaa ja vahingoittaa komponentteja.
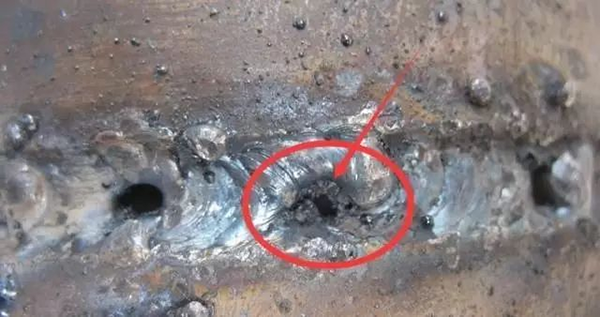
5.2 Syyt:
5.2.1 Hitsin perusmetallia ei ole puhdistettu kunnolla, hitsausvirta on liian pieni, sula metalli jähmettyy liian nopeasti, eikä kuona ehdi kellua ulos.
5.2.2 Hitsauksen perusmetallin ja hitsaustangon kemiallinen koostumus on epäpuhdasta. Jos sulassa altaassa on hitsauksen aikana useita komponentteja, kuten happea, typpeä, rikkiä, fosforia, piitä jne., ei-metallisia kuonasulkeumia muodostuu helposti.
5.2.3 Hitsaaja ei ole ammattitaitoinen ja sauvan kuljetustapa on väärä, jolloin kuona ja sula rauta ovat sekoittuneet ja erottamattomat, mikä estää kuonan kellumisen.
5.2.4 Hitsausurakulma on pieni, hitsaustangon pinnoite irtoaa palasina eikä kaari sulaa; monikerroksisen hitsauksen aikana kuonaa ei puhdisteta kunnolla, eikä kuonaa poisteta ajoissa käytön aikana, mikä kaikki aiheuttaa kuonaa.
5.3 Ennaltaehkäisy- ja valvontatoimenpiteet
5.3.1 Käytä vain hitsaustankoja, joilla on vain hyvä hitsausprosessi, ja hitsatun teräksen tulee täyttää suunnitteluasiakirjojen vaatimukset.
5.3.2 Valitse kohtuulliset hitsausprosessiparametrit hitsausprosessin arvioinnin avulla. Kiinnitä huomiota hitsausuran ja reuna-alueen puhdistukseen. Hitsaustangon ura ei saa olla liian pieni. Monikerroksisissa hitseissä jokaisen hitsikerroksen hitsauskuona on poistettava huolellisesti.
5.3.3 Happamia elektrodeja käytettäessä kuonan tulee olla sulan altaan takana; käytettäessä emäksisiä elektrodeja pystykulmasaumojen hitsaukseen, hitsausvirran oikean valinnan lisäksi on käytettävä lyhytkaarihitsausta. Samanaikaisesti elektrodia tulee liikuttaa oikein, jotta elektrodi heiluu asianmukaisesti niin, että kuona kelluu pintaan.
5.3.4 Käytä esilämmitystä ennen hitsausta, lämmitystä hitsauksen aikana ja eristystä hitsauksen jälkeen, jotta se jäähtyy hitaasti kuonasulkeutumien vähentämiseksi.
6. Huokoisuus
6.1 Ilmiö: Hitsausprosessin aikana sulaan hitsausmetalliin imeytynyt kaasu ei ehdi poistua sulasta altaasta ennen jäähtymistä, vaan se jää hitsin sisään muodostaen reikiä. Huokosten sijainnin mukaan ne voidaan jakaa sisäisiin ja ulkoisiin huokosiin; huokosvirheiden jakautumisen ja muodon mukaan huokosten esiintyminen hitsissä vähentää hitsin lujuutta ja tuottaa myös jännityspitoisuuden, lisää haurautta matalassa lämpötilassa, lämpöhalkeilutaipumusta jne.
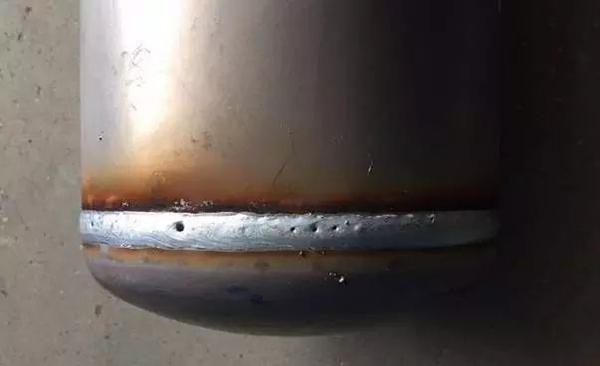
6.2 Syyt
6.2.1 Itse hitsaustangon laatu on huono, hitsaustanko on kostea eikä kuivattu määritettyjen vaatimusten mukaisesti; hitsaustangon pinnoite on kulunut tai irronnut; hitsausydin on ruostunut jne.
6.2.2 Perusmateriaalin sulatuksessa on jäännöskaasua; hitsaustanko ja hitsaus värjäytyvät epäpuhtauksilla, kuten ruosteella ja öljyllä, ja hitsausprosessin aikana syntyy kaasua korkean lämpötilan kaasutuksesta.
6.2.3 Hitsaaja ei ole perehtynyt käyttötekniikkaan tai hänellä on huono näkökyky eikä hän pysty erottamaan sulaa rautaa pinnoitteesta, joten pinnoitteen kaasu sekoittuu metalliliuokseen. Hitsausvirta on liian suuri, mikä tekee hitsaustankosta punaisen ja vähentää suojavaikutusta; kaaren pituus on liian pitkä; virtalähteen jännite vaihtelee liikaa, jolloin kaari palaa epävakaasti jne.
6.3 Ennaltaehkäisy- ja valvontatoimenpiteet
6.3.1 Valitse pätevät hitsaustangot, äläkä käytä hitsauspuikkoja, joissa on halkeamia, kuoriutuneita, kuluneita, epäkeskisiä tai voimakkaasti ruostuneita pinnoitteita. Puhdista öljytahrat ja ruostepisteet hitsin lähellä ja hitsaustangon pinnalla.
6.3.2 Valitse sopiva virta ja säädä hitsausnopeutta. Esilämmitä työkappale ennen hitsausta. Kun hitsaus on valmis tai keskeytetty, kaari tulee vetää hitaasti pois, mikä hidastaa sulan altaan jäähtymisnopeutta ja kaasun poistumista sulassa altaassa välttäen huokosvaurioiden syntymistä.
6.3.3 Vähennä hitsaustyöpaikan kosteutta ja nosta käyttöympäristön lämpötilaa. Ulkona hitsattaessa, jos tuulen nopeus saavuttaa 8 m/s, sadetta, kastetta, lunta jne., ennen hitsausta on suoritettava tehokkaita toimenpiteitä, kuten tuulensuojat ja katokset.
7. Roiskeita ja hitsauskuonaa ei ole puhdistettu hitsauksen jälkeen
7.1 Ilmiö: Tämä on yleisin yleinen ongelma, joka ei ole vain ruma, vaan myös erittäin haitallinen. Sulautuva roiske lisää materiaalipinnan kovettunutta rakennetta ja on helppo aiheuttaa vikoja, kuten kovettumista ja paikallista korroosiota.
7.2 Syyt
7.2.1 Hitsausmateriaalin lääkekuori on kostea ja kulunut varastoinnin aikana tai valittu hitsaustanko ei vastaa perusmateriaalia.
7.2.2 Hitsauslaitteiden valinta ei täytä vaatimuksia, AC- ja DC-hitsauslaitteet eivät vastaa hitsausmateriaaleja, hitsauksen toisiolinjan napaisuuskytkentätapa on virheellinen, hitsausvirta on suuri, hitsausuran reuna on roskien ja öljytahrojen saastuttama, ja hitsausympäristö ei täytä hitsausvaatimuksia.
7.2.3 Käyttäjä ei ole koulutettu eikä toimi ja suojaa määräysten mukaisesti.
7.3 Ennaltaehkäisy- ja valvontatoimenpiteet
7.3.1 Valitse sopiva hitsauslaite hitsauksen perusmateriaalin mukaan.
7.3.2 Hitsauspuikolla tulee olla kuivaus- ja vakiolämpötilalaitteisto sekä kuivaushuoneessa, joka on vähintään 300 mm maasta ja seinästä, on oltava ilmankuivain ja ilmastointilaite. Luo järjestelmä hitsaustankojen vastaanottoa, lähettämistä, käyttöä ja säilytystä varten (erityisesti paineastioita varten).
7.3.3 Puhdista hitsin reuna poistaaksesi kosteuden, öljytahrat ja ruosteen roskista. Talven sadekauden aikana rakennetaan suojavaja hitsausympäristön varmistamiseksi.
7.3.4 Ennen ei-rautametallien ja ruostumattoman teräksen hitsaamista perusmateriaaleille voidaan levittää suojapinnoitteet suojaksi hitsin molemmille puolille. Voit myös valita hitsaustangot, ohuesti pinnoitetut hitsaustangot ja argonsuojan poistamaan roiskeita ja vähentämään kuonaa.
7.3.5 Hitsaus vaatii oikea-aikaista hitsauskuonan puhdistusta ja suojausta.
8. Kaaren arpi
8.1 Ilmiö: Huolimattomasta käytöstä johtuen hitsaustanko tai hitsauskahva koskettaa hitsausta tai maadoitusjohdin koskettaa työkappaletta huonosti aiheuttaen lyhytaikaisen kaaren, jolloin työkappaleen pintaan jää kaariarpi.
8.2 Syy: Sähköhitsauskone on huolimaton eikä suorita suojatoimenpiteitä eikä huolla työkaluja.
8.3 Ennaltaehkäisevät toimenpiteet: Hitsaajien tulee säännöllisesti tarkistaa käytetyn hitsauskahvan johdon ja maadoitusjohdon eristys ja kääriä ne ajoissa, jos ne ovat vaurioituneet. Maadoitusjohto tulee asentaa tukevasti ja luotettavasti. Älä aloita kaaria hitsin ulkopuolella hitsauksen aikana. Hitsauspuristin tulee sijoittaa erilleen perusmateriaalista tai ripustaa asianmukaisesti. Katkaise virransyöttö ajoissa, kun et hitsaa. Jos valokaaren naarmuja löytyy, ne on kiillotettava ajoissa sähköhiomalaikalla. Koska korroosionkestävyysvaatimukset täyttävissä työkappaleissa, kuten ruostumattomassa teräksessä, kaaren arvet tulevat korroosion alkupisteeksi ja heikentävät materiaalin suorituskykyä.
9. Hitsausarvet
9.1 Ilmiö: Jos hitsausarpia ei puhdisteta hitsauksen jälkeen, se vaikuttaa laitteen makroskooppiseen laatuun ja virheellinen käsittely aiheuttaa myös pintahalkeamia.
9.2 Syy: Epätyypillisten laitteiden valmistuksen ja asennuksen aikana kohdistuvat hitsauskiinnittimet aiheutuvat, kun ne poistetaan valmistumisen jälkeen.
9.3 Ennaltaehkäisevät toimenpiteet: Asennusprosessissa käytetyt nostolaitteet tulee kiillottaa hiomalaikalla, jotta ne ovat irrotuksen jälkeen tasapinnassa perusmateriaalin kanssa. Älä käytä vasaraa kiinnikkeiden lyömiseen, jotta perusmateriaali ei vaurioidu. Sähköhitsauksen aikana liian syvät kaarikuopat ja naarmut tulee korjata ja kiillottaa hiomalaikalla niin, että ne ovat tasossa perusmateriaalin kanssa. Kunhan kiinnität huomiota käytön aikana, tämä vika voidaan poistaa.
10. Epätäydellinen tunkeutuminen
10.1 Ilmiö: Hitsauksen aikana hitsin juuri ei ole täysin sulautunut perusmateriaaliin tai perusmateriaali ja perusmateriaali hitsautuvat osittain epätäydellisesti. Tätä vikaa kutsutaan epätäydelliseksi tunkeutumiseksi tai epätäydelliseksi fuusioksi. Se heikentää liitoksen mekaanisia ominaisuuksia ja aiheuttaa jännityskeskittymiä ja halkeamia tälle alueelle. Hitsauksessa mikään hitsaus ei saa olla epätäydellistä.
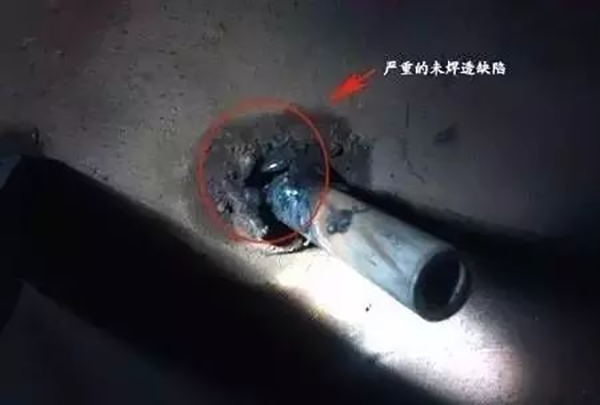
10.2 Syyt
10.2.1 Uraa ei ole käsitelty määräysten mukaisesti, tylpän reunan paksuus on liian suuri ja uran kulma tai kokoonpanon rako liian pieni.
10.2.2 Kaksipuolisessa hitsauksessa takajuurta ei puhdisteta perusteellisesti tai uran sivuja ja välihitsausta ei puhdisteta, jolloin oksidit, kuona jne. estävät metallien täydellisen sulautumisen.
10.2.3 Hitsaaja ei ole ammattitaitoinen. Esimerkiksi kun hitsausvirta on liian suuri, pohjamateriaali ei ole sulanut, mutta hitsaustanko on sulanut, joten perusmateriaali ja hitsaustankoon kerrostettu metalli eivät ole sulautuneet yhteen; kun virta on liian pieni; hitsaustangon nopeus on liian nopea, perusmateriaalia ja hitsaustankoon kerrostettua metallia ei voida sulattaa hyvin; toiminnassa hitsaustangon kulma on väärä, sulatus on vinoutunut toiselle puolelle tai hitsauksen aikana tapahtuu puhallusilmiö, joka aiheuttaa epätäydellisen tunkeutumisen, jossa kaari ei voi toimia.
10.3 Ennaltaehkäisevät toimenpiteet
10.3.1 Käsittele ja kokoa rako suunnittelupiirustuksessa tai spesifikaatiostandardissa määritellyn urakoon mukaan.
Postitusaika: 28.7.2024