Huokoisuus, ontelotyyppiset epäjatkuvuudet, jotka muodostuvat kaasun juuttumisesta jähmettymisen aikana, on yleinen, mutta hankala vika MIG-hitsauksessa, ja siihen on useita syitä. Se voi esiintyä puoliautomaattisissa tai robottisovelluksissa ja vaatii molemmissa tapauksissa poistamista ja uudelleenkäsittelyä, mikä johtaa seisokkeihin ja kustannusten nousuun.
Teräshitsauksen huokoisuuden suurin syy on typpi (N2), joka joutuu hitsausaltaaseen. Kun nestealtaan jäähtyy, N2:n liukoisuus vähenee merkittävästi ja N2 tulee ulos sulasta teräksestä muodostaen kuplia (huokosia). Galvanoidussa/galvannealihitsauksessa haihtunut sinkki voidaan sekoittaa hitsausaltaaseen, ja jos ei ole tarpeeksi aikaa poistua ennen altaan jähmettymistä, se muodostaa huokoisuutta. Alumiinin hitsauksessa kaiken huokoisuuden aiheuttaa vety (H2), samalla tavalla kuin N2 toimii teräksessä.
Hitsaushuokoisuus voi ilmetä ulkoisesti tai sisäisesti (kutsutaan usein pinnanalaiseksi huokoiseksi). Se voi kehittyä myös yhteen kohtaan hitsauksessa tai koko pituudelta, mikä johtaa heikkoihin hitseihin.
Huokoisuuden tärkeimpien syiden tunnistaminen ja niiden nopea ratkaiseminen voi parantaa laatua, tuottavuutta ja tulosta.
Huono suojakaasun kattavuus
Huono suojakaasupeitto on yleisin syy hitsaushuokoisuuteen, koska se mahdollistaa ilmakaasujen (N2 ja H2) saastuttamisen hitsausaltaassa. Oikean peiton puute voi johtua useista syistä, mukaan lukien, mutta ei rajoittuen, huono suojakaasun virtausnopeus, vuodot kaasukanavassa tai liiallinen ilmavirtaus hitsauskennossa. Myös liian nopeat ajonopeudet voivat olla syyllisiä.
Jos käyttäjä epäilee huonon virtauksen aiheuttavan ongelman, yritä säätää kaasun virtausmittaria varmistaaksesi, että nopeus on riittävä. Käytettäessä esimerkiksi ruiskutussiirtotilaa 35-50 kuutiojalkaa tunnissa (cfh) virtauksen pitäisi riittää. Hitsaus suuremmilla ampeerimäärillä vaatii virtausnopeuden lisäämistä, mutta on tärkeää, ettei nopeutta aseteta liian suureksi. Tämä voi aiheuttaa turbulenssia joissakin pistoolirakenteissa, mikä häiritsee suojakaasun peittoa.
On tärkeää huomata, että eri tavalla suunnitelluilla aseilla on erilaiset kaasuvirtausominaisuudet (katso kaksi esimerkkiä alla). Ylämallin kaasun virtausnopeuden "sweet spot" on paljon suurempi kuin alamallin. Tämä on asia, joka hitsausinsinöörin on otettava huomioon hitsauskennoa asentaessaan.
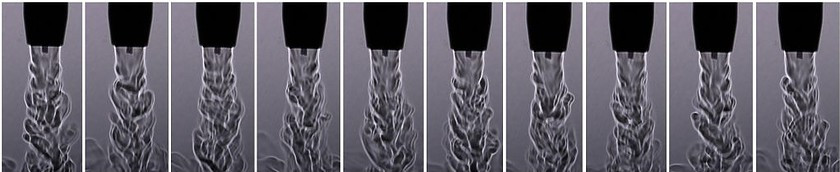
Malli 1 näyttää tasaisen kaasun virtauksen suuttimen ulostulossa
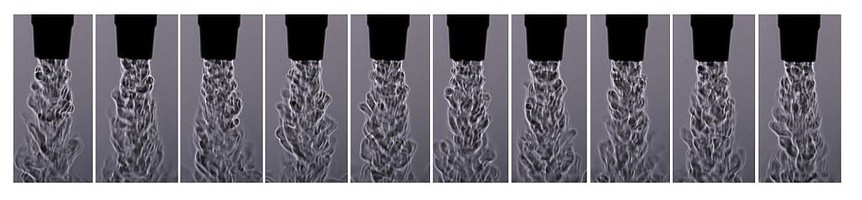
Malli 2 esittää turbulenttia kaasuvirtausta suuttimen ulostulossa.
Tarkista myös vaurioiden varalta kaasuletkussa, liittimissä ja liittimissä sekä MIG-hitsauspistoolin virtanastan O-renkaissa. Vaihda tarvittaessa.
Kun käytät puhaltimia käyttäjien tai hitsauskennon osien jäähdyttämiseen, varmista, etteivät ne ole suunnattu suoraan hitsausalueelle, jossa ne voivat häiritä kaasun peittoa. Aseta suojus hitsauskennoon suojaamaan ulkoiselta ilmavirralta.
Kosketa ohjelmaa uudelleen robottisovelluksissa varmistaaksesi, että kärjestä työskentelyyn on oikea etäisyys, joka on tyypillisesti ½–3/4 tuumaa kaaren halutusta pituudesta riippuen.
Lopuksi hidasta kulkunopeutta, jos huokoisuus jatkuu, tai ota yhteyttä MIG-pistoolin toimittajaan erilaisten etuosan komponenttien saamiseksi, joilla on parempi kaasupeitto.
Epäjalometallin kontaminaatio
Perusmetallin saastuminen on toinen syy huokoisuuden esiintymiseen – öljystä ja rasvasta myllyhilseen ja ruosteeseen. Kosteus voi myös edistää tätä epäjatkuvuutta, erityisesti alumiinin hitsauksessa. Tämäntyyppiset epäpuhtaudet johtavat tyypillisesti ulkoiseen huokoisuuteen, joka näkyy käyttäjälle. Galvanoitu teräs on alttiimpi pinnan huokoisuudelle.
Ulkoisen huokoisuuden estämiseksi muista puhdistaa pohjamateriaali perusteellisesti ennen hitsausta ja harkita metallisydänhitsauslangan käyttöä. Tämän tyyppisessä langassa on enemmän hapettumisenestoaineita kuin kiinteässä langassa, joten se sietää paremmin perusmateriaaliin jääviä epäpuhtauksia. Säilytä näitä ja muita johtimia aina kuivassa, puhtaassa paikassa, jonka lämpötila on sama tai hieman korkeampi kuin laitoksen. Tämä auttaa minimoimaan kondensoitumisen, joka voi viedä kosteutta hitsausaltaaseen ja aiheuttaa huokoisuutta. Älä säilytä johtoja kylmässä varastossa tai ulkona.
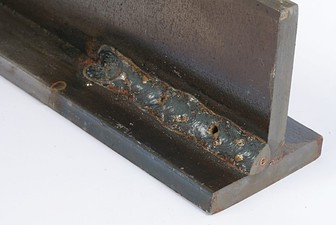
Huokoisuus, ontelotyyppiset epäjatkuvuudet, jotka muodostuvat kaasun juuttumisesta jähmettymisen aikana, on yleinen, mutta hankala vika MIG-hitsauksessa, ja siihen on useita syitä.
Galvanoitua terästä hitsattaessa sinkki höyrystyy alemmassa lämpötilassa kuin teräs sulaa, ja nopeat kulkunopeudet saavat hitsausaltaan jäätymään nopeasti. Tämä voi vangita sinkkihöyryä teräkseen, mikä johtaa huokoisuuteen. Taistele tätä tilannetta valvomalla ajonopeutta. Harkitse jälleen erityisesti suunniteltua (virtauskaava) metallisydänlankaa, joka edistää sinkkihöyryn poistumista hitsausaltaalta.
Tukkeutuneet ja/tai alamittaiset suuttimet
Tukkeutuneet ja/tai alamittaiset suuttimet voivat myös aiheuttaa huokoisuutta. Hitsausroiskeet voivat kerääntyä suuttimeen ja kosketinkärjen ja diffuusorin pinnalle, mikä rajoittaa suojakaasun virtausta tai saa sen turbulenssiksi. Molemmat tilanteet jättävät hitsausaltaan riittämättömäksi.
Tilannetta vaikeuttaa suutin, joka on liian pieni sovellukseen ja alttiimpi suuremmalle ja nopeammalle roiskeen muodostumiselle. Pienemmät suuttimet voivat tarjota paremman pääsyn liitoksiin, mutta myös estää kaasun virtauksen, koska kaasuvirtaukselle sallitaan pienempi poikkileikkauspinta-ala. Pidä aina mielessä kosketuskärjen ja suuttimen ulkoneman (tai syvennyksen) muuttuja, koska tämä voi olla toinen tekijä, joka vaikuttaa suojakaasun virtaukseen ja huokoisuuteen suuttimen valinnassa.
Tämä mielessä pitäen varmista, että suutin on riittävän suuri sovellusta varten. Tyypillisesti sovelluksissa, joissa on suuri hitsausvirta ja joissa käytetään suurempia lankakokoja, tarvitaan suutin, jolla on suurempi reikä.
Puoliautomaattisissa hitsaussovelluksissa tarkasta ajoittain hitsausroiskeet suuttimessa ja poista ne hitsauspihdeillä (hitsauspihdeillä) tai vaihda suutin tarvittaessa. Varmista tämän tarkastuksen aikana, että kontaktikärki on hyvässä kunnossa ja että kaasuhajottimessa on tyhjät kaasuportit. Käyttäjät voivat myös käyttää roiskenestomassaa, mutta heidän tulee varoa upottamasta suutinta seokseen liian pitkälle tai liian pitkäksi aikaa, koska liiallinen seos voi saastuttaa suojakaasun ja vaurioittaa suuttimen eristystä.
Investoi robottihitsauksessa suuttimien puhdistusasemaan tai kalvimeen roiskeiden kertymisen estämiseksi. Tämä oheislaite puhdistaa suuttimen ja diffuusorin rutiininomaisten tuotannon taukojen aikana, jotta se ei vaikuta syklin aikaan. Suuttimien puhdistusasemat on tarkoitettu toimimaan yhdessä roiskesuihkeen kanssa, joka levittää ohuen kerroksen seosta etuosien päälle. Liian paljon tai liian vähän roiskenestettä voi lisätä huokoisuutta. Ilmapuhalluksen lisääminen suuttimien puhdistusprosessiin voi myös auttaa poistamaan irtonaisia roiskeita kulutustarvikkeista.
Laadun ja tuottavuuden ylläpitäminen
Hitsausprosessin tarkkailu ja huokoisuuden syyt tuntemalla ratkaisut on suhteellisen yksinkertaista toteuttaa. Tämä voi auttaa varmistamaan pidemmän valokaaren syttymisajan, laadukkaat tulokset ja enemmän hyviä osia siirtymään tuotannon läpi.
Postitusaika: 2.2.2020